Crafting Excellence for Optimal Pellet Production
High-Performance SERVODAY Pellet Mill Rollers for Biomass & Wood Pellets
Explore high-performance SERVODAY Pellet Mill Rollers designed for durability and efficiency in biomass and wood pellet production. Precision-engineered for superior performance
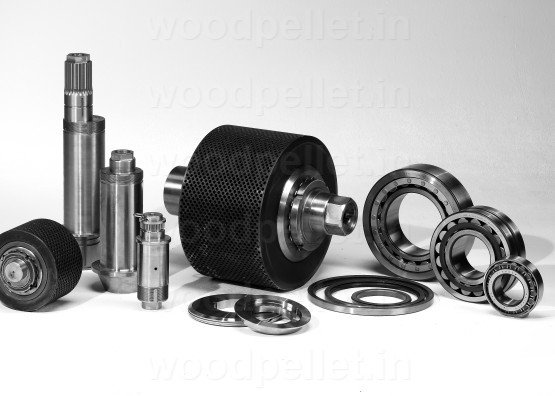
High-Performance Rollers for Enhanced Pellet Production
Maximize Pellet Mill Efficiency with SERVODAY Rollers
SERVODAY Rollers for Pellet Mills are engineered to deliver top-notch performance in pellet production. Designed specifically for biomass and wood pellets, these rollers ensure smooth and efficient operation, enhancing the productivity of your pellet mill. With high precision and durability, SERVODAY Rollers help achieve optimal pellet quality and reduce downtime, making them a vital component in your pellet production process.
Superior Durability and Longevity
Robust Construction for Long-Lasting Performance from SERVODAY
Constructed from high-grade materials, SERVODAY Rollers are built to withstand the rigorous demands of continuous pellet production. Their robust design ensures longevity and reliable performance, even under heavy loads and high-pressure conditions. This durability translates to fewer replacements and lower maintenance costs, providing a cost-effective solution for pellet mill operations.
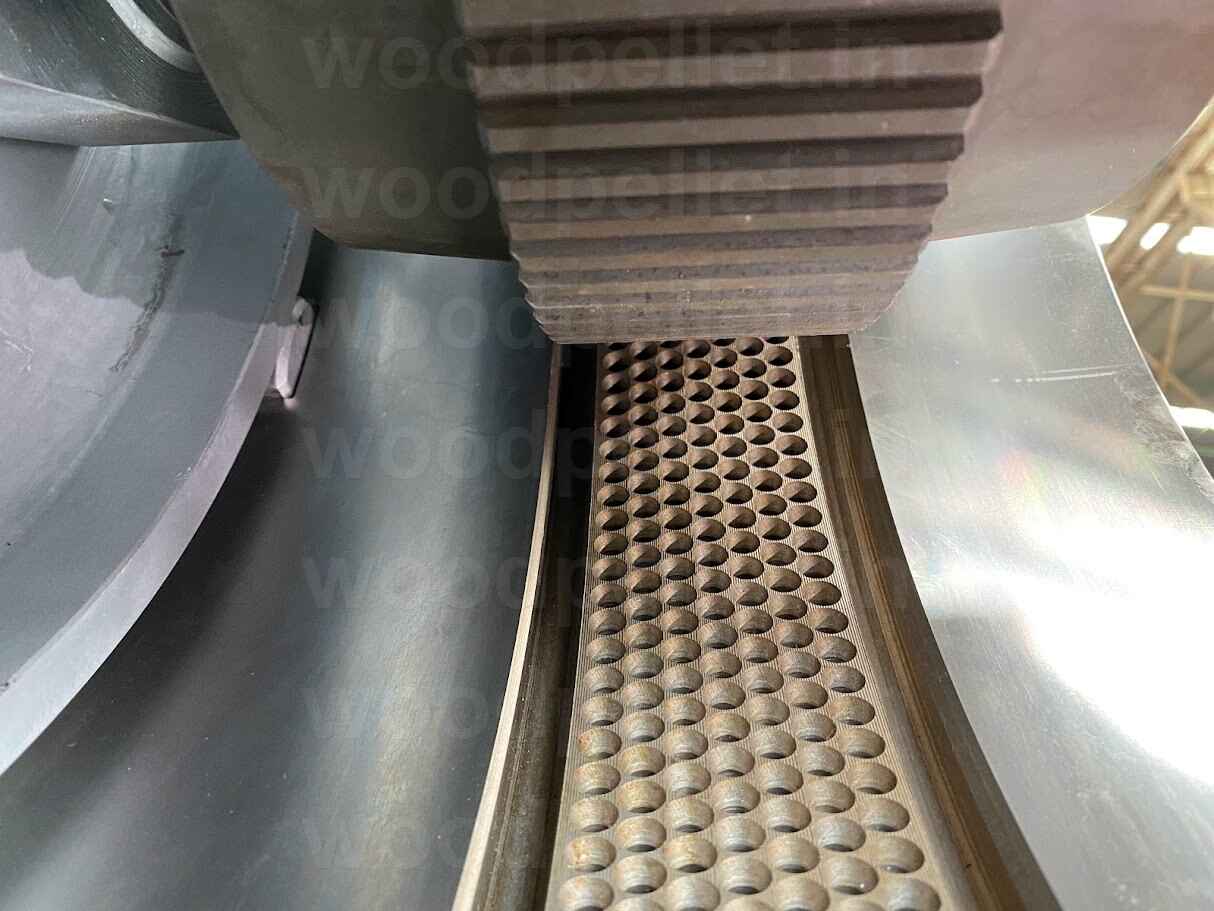
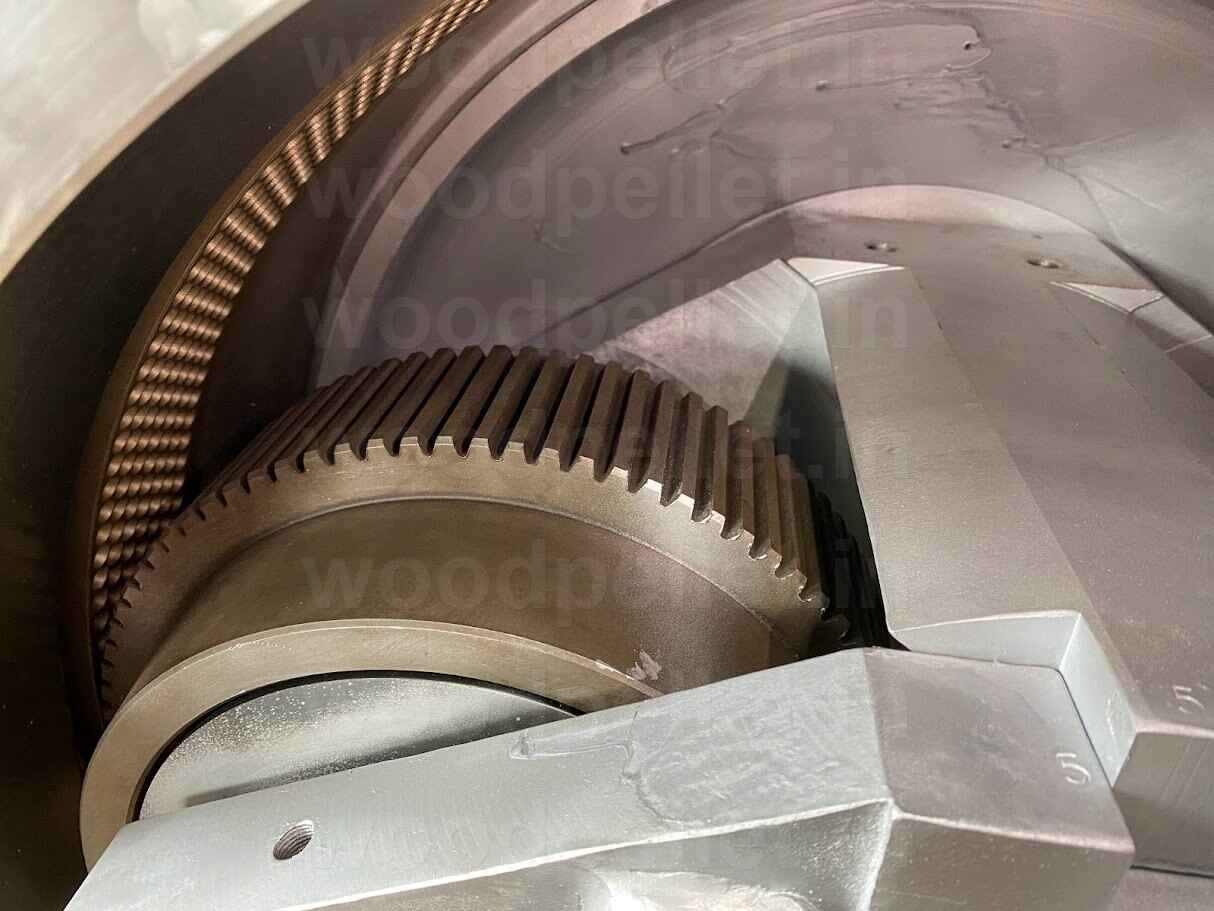
Advanced Engineering for Optimal Compression
Tailored Compression for Diverse Biomass Materials
SERVODAY Rollers are meticulously engineered to offer optimal compression for various types of biomass and wood materials. Whether dealing with hardwood, softwood, or agricultural residues, our rollers are designed to handle different densities and moisture levels, ensuring consistent pellet quality. The precise engineering of these rollers allows for the efficient processing of diverse materials, enhancing overall pellet production.
Technical Excellence for Efficient Operation
Precision Manufacturing for Seamless Integration
Our rollers are manufactured with precision to ensure seamless integration with SERVODAY Pellet Mills. The advanced design includes features such as uniform roller surfaces and optimized roller diameter, which contribute to the efficient compaction of materials and smooth pellet formation. This technical excellence minimizes friction and wear, extending the lifespan of both the rollers and the pellet mill itself.
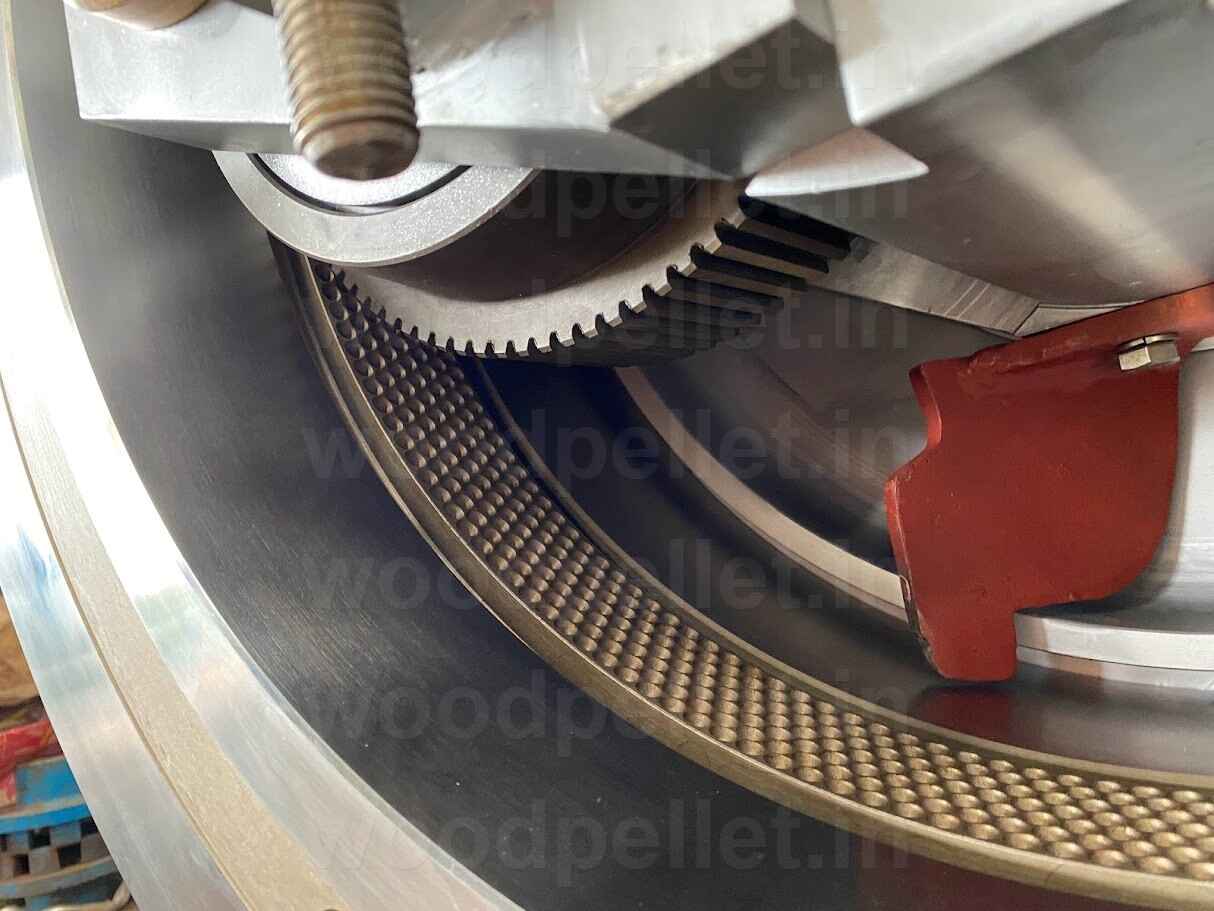
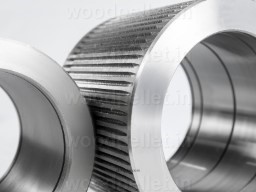
Versatile Applications Across Industries
Adaptable Solutions for Various Pellet Production Needs
SERVODAY Rollers are versatile and suitable for a wide range of applications in the pellet production industry. From producing biomass fuel pellets to manufacturing animal feed pellets, these rollers offer adaptability and high performance. Their ability to handle different types of materials and operating conditions makes them an essential component for any pellet production facility, ensuring consistent and high-quality output.
Superior Craftsmanship in SERVODAY Pellet Mill Rollers
Premium materials and precision engineering ensure exceptional performance for SERVODAY Pellet Mill Rollers. Starting with meticulously inspected alloy steel blanks, automated machining processes shape each roller to exact specifications. Advanced hardening treatments increase surface durability, while specialized grooving optimizes pellet compression. Comprehensive quality checks throughout production guarantee full traceability and peak performance, making SERVODAY Pellet Mill Rollers highly dependable for rigorous pelletizing tasks.
Premium Alloy Steel for Maximum Strength
The creation of SERVODAY Pellet Mill Rollers begins with top-quality alloy steel blanks. These blanks are chosen for their superior durability and wear resistance. Each blank undergoes stringent inspections to meet our high-quality standards. By maintaining a robust inventory of alloy steel, we ensure quick production times and consistent availability of our products.
Precision Machining for Custom Roller Profiles
The machining phase is crucial for forming SERVODAY Pellet Mill Rollers into their final shapes. Using advanced, fully automated machinery, we achieve high precision and consistency in our rollers. This automation enables rapid production while maintaining exceptional quality, ensuring each roller is tailored to the specific requirements of our customers.
Advanced Hardening for Enhanced Durability
Hardening is a key component in the manufacturing process of SERVODAY Pellet Mill Rollers. We utilize advanced heat treatment techniques to enhance the surface hardness of the rollers, boosting their wear resistance and overall durability. This ensures that the rollers can endure the high pressures and abrasive conditions of pellet production, significantly extending their operational lifespan.
Specialized Grooving for Optimal Pellet Formation
Grooving is a vital step in the production of SERVODAY Pellet Mill Rollers. This process involves creating grooves on the roller surface, tailored to optimize pellet formation and compression. The grooving patterns can be adjusted to meet specific requirements, achieving desired pellet quality and production efficiency.
Rigorous Quality Control for Consistent Excellence
Quality control is a cornerstone of the SERVODAY Pellet Mill Rollers manufacturing process. We perform inspections at every stage, with particular focus on the post-hardening phase. Each roller is marked with detailed specifications, including material composition and dimensions, ensuring full traceability and compliance with our quality standards. This thorough quality control ensures every roller meets the highest standards of performance and reliability.
Dependability for Demanding Applications
SERVODAY Pellet Mill Rollers are engineered to meet the most stringent productivity and durability requirements. Our technical expertise and meticulous production processes ensure each roller is robust and reliable, capable of withstanding high-pressure applications in biomass and wood pellet production. By providing superior rollers, we help our customers achieve optimal pellet quality and efficient production.
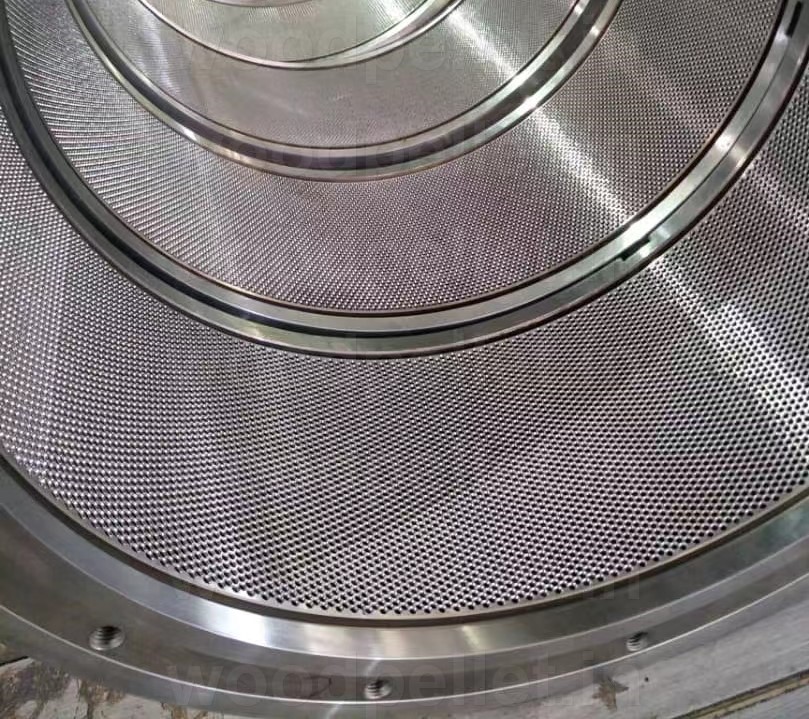