Optimizing Biomass and Wood Pellet Production with SERVODAY Ring Die Pellet Mill
Learn about efficient pelletization with SERVODAY Ring Die Pellet Mill: raw material, moisture, size, distribution, and pre-processing techniques.
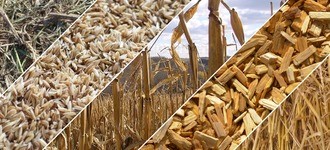
Revolutionizing Crop Residue Utilization
Raw Material Size Requirements
For optimal pelletization with SERVODAY Ring Die Pellet Mill, biomass and wood raw materials must adhere to specific size criteria. Typically, particles or chips ranging from 3 to 8 millimeters in diameter ensure uniform feeding into the pellet mill. This uniformity promotes even distribution within the die, yielding high-quality pellets with consistent dimensions and enhanced efficiency.
Revolutionizing Crop Residue Utilization
Moisture Content
Maintaining an ideal moisture content of 10% to 15% is crucial for efficient pellet production with SERVODAY Ring Die Pellet Mill. Excess moisture can lead to handling issues and poor pellet quality, while insufficient moisture hampers binding and durability. Optimal moisture levels ensure proper compaction and pellet integrity, maximizing efficiency and product quality.
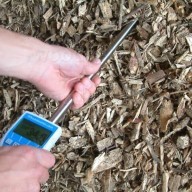
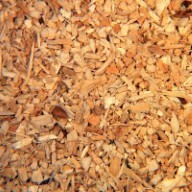
Revolutionizing Crop Residue Utilization
Particle Size Distribution
Achieving a balanced particle size distribution is essential for optimal pelletization with SERVODAY Ring Die Pellet Mill. A mix of fines, fibers, and coarse particles facilitates proper compaction and binding, resulting in pellets with improved structural integrity. This heterogeneous mixture enhances pellet quality and mechanical strength, enhancing overall efficiency.
Need Answers on Wood and Biomass Pellets: Cost, Quality, and Ecological Benefits
What Is Cheaper: Pellets or Coal Fuel? - Coal Fuel or Pellet Fuel - What Is Wood and Biomass Pellet Fuel? - Colour Versus Quality of Pellets - How to Recognise Good Wood and Biomass Pellets? - Why Is Pellet Ecological?
Revolutionizing Crop Residue Utilization
Foreign Matter and Contaminants
To safeguard equipment integrity and ensure consistent pellet quality with SERVODAY Ring Die Pellet Mill, biomass and wood raw materials must be free from foreign matter and contaminants. Thorough screening and removal of contaminants prevent equipment wear and blockages, enabling uninterrupted pellet production and maximizing efficiency.
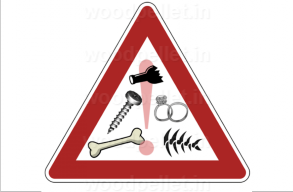
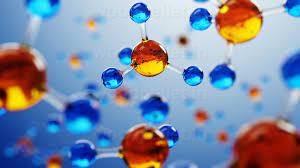
Revolutionizing Crop Residue Utilization
Chemical Composition
The chemical composition of biomass and wood raw materials impacts pelletization efficiency and product quality with SERVODAY Ring Die Pellet Mill. A balanced composition of cellulose, hemicellulose, and lignin provides binding properties and structural integrity to pellets. Low ash and moisture content, along with consistent calorific value, contribute to efficient combustion and optimal pellet performance.
Revolutionizing Crop Residue Utilization
Pre-Processing and Conditioning
Pre-processing and conditioning may be necessary to optimize raw materials for pelletization with SERVODAY Ring Die Pellet Mill. Size reduction, drying, and the addition of binders enhance pellet quality and performance. Proper pre-processing ensures raw materials meet criteria for efficient pelletization, resulting in high-quality pellets with consistent properties.
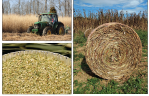
Experience Unmatched Cost-to-Performance Ratio with SERVODAY Ring Die Pellet Mill Machines
Are you ready to elevate your pelletizing process to new heights? Contact us today to request a quote for our advanced SERVODAY Ring Die Pellet Mill Machines. Discover the perfect solution tailored to your pelletizing needs, offering a customized quote that aligns with your budget and requirements.
Optimizing Biomass and Wood Pellet Production with SERVODAY Ring Die Pellet Mill
Maximize profits and achieve ENplus Standard quality with SERVODAY's advanced Ring Die Pellet Mill Machines and optimal pellet recipes for biomass materials
EFFICIENCY, REALIABILITY & ADVANTAGES
Empower Your Biomass Processing Journey with SERVODAY: Unleashing the Power of Ring Die Pellet Mill Machine Innovation
BIOMASS MIX RECEIPS
Unlocking Value with SERVODAY's Expert Formulations: Maximize Profits with Optimal Pellet Recipes by SERVODAY for Biomass Materials
ENplus: Driving Quality
Engineered for ENplus Standard Compliance: Achieve ENplus Standard Quality with SERVODAY's Ring Die Pellet Mill Machines