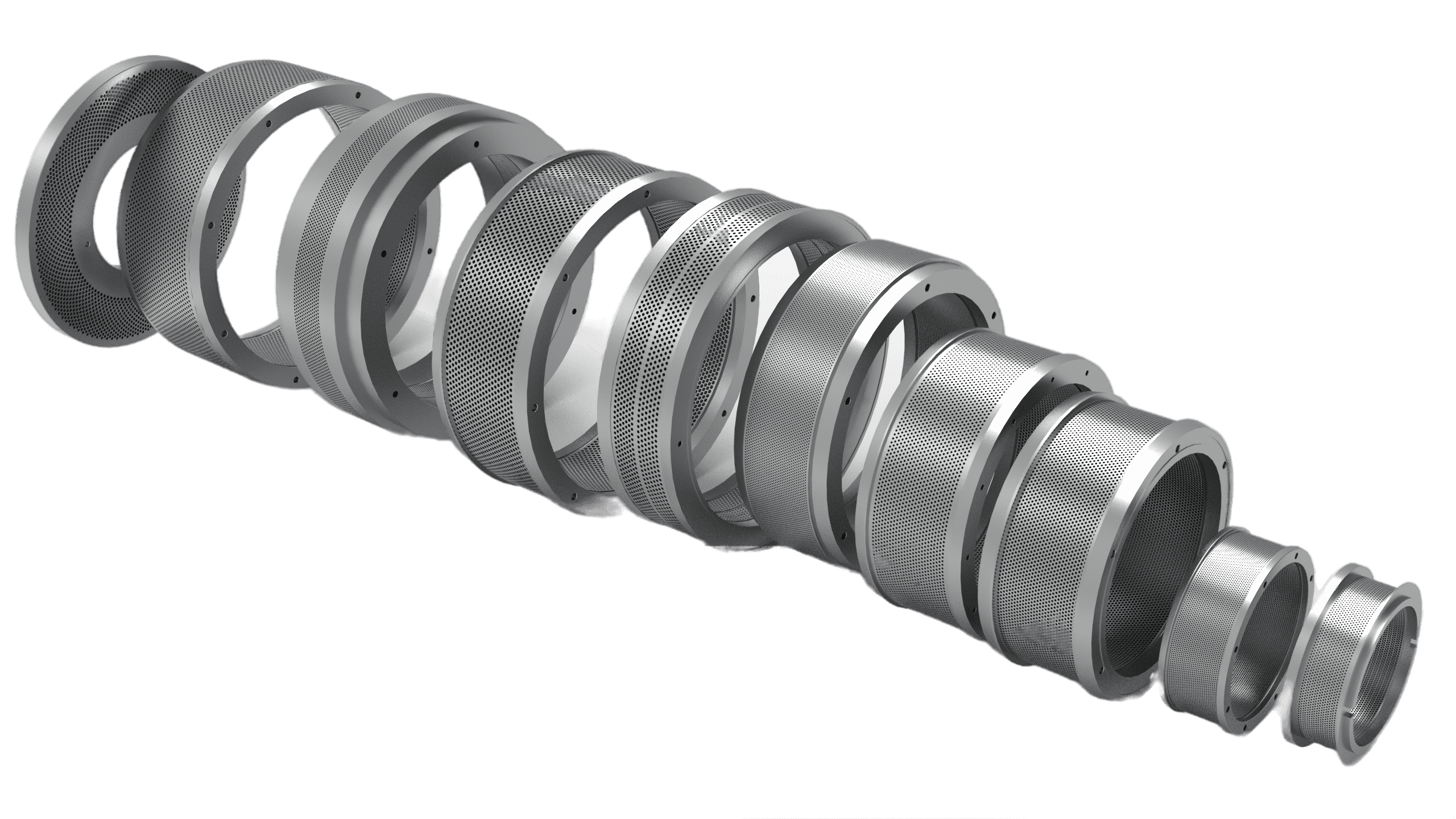
Ring Die Engineering FAQ: Expert Answers on SERVODAY Wood & Biomass Machinery
Unlock expert insights on ring die engineering for wood & biomass machinery like SERVODAY Pellet Mills. Discover tips for efficient pellet production.
RING DIE ENGINEERING
1
What factors determine the compression ratio of a SERVODAY Ring Die Pellet Mill Machines die?
The compression ratio of a SERVODAY Ring Die Pellet Mill Machines die is determined by factors such as hole size, thickness of the die, taper of the bell mouth, material, and hardness.
2
What are the standard hole sizes for SERVODAY Ring Die Pellet Mill Machines dies?
The standard hole sizes for SERVODAY Ring Die Pellet Mill Machines dies are typically 6mm, 8mm, and 10mm.
3
How does the thickness of a SERVODAY Ring Die Pellet Mill Machines die affect pellet production?
The thickness of a SERVODAY Ring Die Pellet Mill Machines die impacts the molding effect. Thicker dies result in longer molding times, higher pellet density, and higher extrusion strength, while thinner dies may lead to easier breakage, lower pellet density, and higher production with lower molding rates.
4
What does the compression ratio indicate in SERVODAY Ring Die Pellet Mill Machines dies?
The compression ratio of a SERVODAY Ring Die Pellet Mill Machines die reflects the ratio of effective hole length to the minimum hole diameter. It indicates the extrusion force of the wood pellet machine.
5
How is the compression ratio calculated for SERVODAY Ring Die Pellet Mill Machines?
The compression ratio for SERVODAY Ring Die Pellet Mill Machines is calculated by dividing the effective hole length by the minimum hole diameter of the die.
6
Why is the compression ratio important in pellet production using SERVODAY Ring Die Pellet Mill Machines?
The compression ratio determines the molding effects of wood pellets when using SERVODAY Ring Die Pellet Mill Machines. It affects factors such as pellet strength, density, and production rate.
7
What materials are commonly used to manufacture SERVODAY Ring Die Pellet Mill Machines dies?
SERVODAY Ring Die Pellet Mill Machines dies are typically made of carbon steel, alloy structural steel, or stainless steel.
8
What is the significance of the effective length in SERVODAY Ring Die Pellet Mill Machines dies?
The effective length in SERVODAY Ring Die Pellet Mill Machines dies is the portion of the die thickness that actually performs work on the feed material, influencing pellet compactness and quality.
9
How does the L/D ratio affect SERVODAY Ring Die Pellet Mill Machines dies?
The L/D ratio, which is the effective length divided by the hole diameter, influences pellet die resistance in SERVODAY Ring Die Pellet Mill Machines. Higher L/D ratios provide greater resistance, while lower ratios offer less resistance.
10
What is the importance of selecting suitable SERVODAY Ring Die Pellet Mill Machines dies for different types of feed?
Selecting appropriate dies for SERVODAY Ring Die Pellet Mill Machines according to feed formulation is crucial for achieving desired pellet quality, reducing die wear, and optimizing production efficiency.
11
How does SERVODAY Ring Die Pellet Mill Machines offer solutions for different feed types?
SERVODAY Ring Die Pellet Mill Machines provide customizable die options suitable for various feed formulations, ensuring optimal pellet quality and production efficiency.
12
How does the material composition affect the selection of SERVODAY Ring Die Pellet Mill Machines dies?
The material composition of the feed influences die selection for SERVODAY Ring Die Pellet Mill Machines, as different materials require different compression ratios and die configurations.
13
Why is it important to adjust the gap between the SERVODAY Ring Die Pellet Mill Machines die and roller shells?
Proper adjustment of the gap ensures optimal pellet production with SERVODAY Ring Die Pellet Mill Machines by preventing uneven wear and ensuring efficient pellet formation.
14
What factors affect the life of SERVODAY Ring Die Pellet Mill Machines dies and roller shells?
Factors such as feed formulation, raw material characteristics, moisture content, operator skill, and maintenance practices influence the lifespan of SERVODAY Ring Die Pellet Mill Machines dies and roller shells.
15
What are the advantages of stainless steel high chrome dies over mild steel dies for SERVODAY Ring Die Pellet Mill Machines?
Stainless steel high chrome dies for SERVODAY Ring Die Pellet Mill Machines offer advantages such as longer lifespan, better pellet strength, immediate start-up, and reduced maintenance costs compared to mild steel dies.
16
Why does stainless steel high chrome grade attract magnets in SERVODAY Ring Die Pellet Mill Machines?
Stainless steel high chrome grade attracts magnets in SERVODAY Ring Die Pellet Mill Machines due to its martensitic crystal structure, which contains iron and exhibits magnetic properties.
17.
Can SERVODAY Ring Die Pellet Mill Machines dies be repaired?
Yes, SERVODAY Ring Die Pellet Mill Machines dies can be re-countered if the counters have worn out prematurely, affecting pellet quality and production efficiency.
18
What is the main reason for SERVODAY Ring Die Pellet Mill Machines die rollover?
SERVODAY Ring Die Pellet Mill Machines die rollover occurs due to factors such as excessive roll-to-die proximity, wear ring play, and main bearing play, leading to reduced production efficiency and increased machine wear.
19
Why is Pellet Durability Index (PDI) significant in pellet quality for SERVODAY Ring Die Pellet Mill Machines?
PDI measures pellet durability and is crucial for evaluating pellet quality when using SERVODAY Ring Die Pellet Mill Machines, with lower PDIs indicating greater pellet fragility and reduced final output.
20
What are the different types of relief used in SERVODAY Ring Die Pellet Mill Machines dies?
Relief types for SERVODAY Ring Die Pellet Mill Machines include no relief, straight or single step relief, dual step relief, variable relief, staggered relief, and tapered relief, each serving specific purposes in pellet production.
21
How do you choose the compression ratio for SERVODAY Ring Die Pellet Mill Machines?
The compression ratio for SERVODAY Ring Die Pellet Mill Machines should be selected based on raw material composition, product requirements, and production considerations.
22
What materials are commonly used to manufacture ring dies for SERVODAY Pellet Mill Machines?
Ring dies for SERVODAY Pellet Mill Machines are typically made of carbon steel, alloy structural steel, or stainless steel, depending on factors such as material corrosion and working strength.
23
Why is the diameter of the SERVODAY Ring Die Pellet Mill Machines die important?
The diameter of the SERVODAY Ring Die Pellet Mill Machines die influences pellet size and production efficiency, with different hole sizes suitable for various types of feed and raw materials.
24
How does the compression ratio affect pellet output in SERVODAY Ring Die Pellet Mill Machines?
Higher compression ratios in SERVODAY Ring Die Pellet Mill Machines result in stronger, denser pellets with lower production rates, while lower compression ratios produce looser pellets with higher production rates.
25
What are the implications of die relief damage for SERVODAY Ring Die Pellet Mill Machines?
Die relief damage in SERVODAY Ring Die Pellet Mill Machines can lead to decreased pellet quality, increased wear on the die, and reduced production efficiency, necessitating timely repairs and maintenance.
26
How does die wear affect the performance of SERVODAY Ring Die Pellet Mill Machines?
Excessive die wear in SERVODAY Ring Die Pellet Mill Machines can result in reduced pellet quality, uneven pellet size, and decreased production efficiency, highlighting the importance of regular maintenance and monitoring.
27
Why is it important to monitor and adjust the gap between rollers and dies in SERVODAY Ring Die Pellet Mill Machines operation?
Proper adjustment of the gap ensures uniform pellet compression, optimal pellet quality, and efficient production rates with SERVODAY Ring Die Pellet Mill Machines, minimizing wear on the die and rollers.
28
What measures can be taken to prevent die rollover in SERVODAY Ring Die Pellet Mill Machines operation?
Regular maintenance schedules, proper die alignment, and monitoring of roll-to-die proximity can help prevent die rollover and associated production disruptions in SERVODAY Ring Die Pellet Mill Machines operations.
29
How does die relief contribute to the operation of SERVODAY Ring Die Pellet Mill Machines?
Die relief facilitates the smooth exit of pellets from the die holes in SERVODAY Ring Die Pellet Mill Machines, reducing friction and wear on the die surface while promoting consistent pellet quality and production efficiency.
30
What role does die temperature play in SERVODAY Ring Die Pellet Mill Machines operation?
Proper die temperature control is crucial in SERVODAY Ring Die Pellet Mill Machines to prevent issues such as reduced pellet density, increased wear on the die surface, and decreased production efficiency.
31
How does the material composition of the die affect its durability in SERVODAY Ring Die Pellet Mill Machines?
Die materials with higher chromium content offer superior wear resistance and durability in SERVODAY Ring Die Pellet Mill Machines, reducing the frequency of die replacement and maintenance in high-volume pellet production operations.
32
What are the consequences of improper die alignment in SERVODAY Ring Die Pellet Mill Machines operation?
Improper die alignment in SERVODAY Ring Die Pellet Mill Machines can lead to issues such as increased wear on the die and rollers, uneven pellet quality, reduced production efficiency, and higher energy consumption.
33
What factors should be considered when selecting the appropriate compression ratio for pellet production using SERVODAY Ring Die Pellet Mill Machines?
Factors such as raw material composition, pellet quality requirements, production volume, and die specifications should be considered when determining the optimal compression ratio for pellet production using SERVODAY Ring Die Pellet Mill Machines.
34
How does die wear affect pellet quality and production efficiency in SERVODAY Ring Die Pellet Mill Machines operation?
Excessive die wear in SERVODAY Ring Die Pellet Mill Machines can lead to issues such as uneven pellet size, reduced pellet density, and increased energy consumption, negatively impacting pellet quality and production efficiency.
35
Why is it important to monitor and adjust the gap between the rollers and die in SERVODAY Ring Die Pellet Mill Machines operation?
Proper adjustment of the gap between the rollers and die in SERVODAY Ring Die Pellet Mill Machines ensures uniform pellet compression, optimal pellet quality, and efficient production rates, minimizing wear on the die and rollers.
36
What role does die relief play in SERVODAY Ring Die Pellet Mill Machines operation?
Die relief in SERVODAY Ring Die Pellet Mill Machines facilitates the smooth exit of pellets from the die holes, reducing friction and wear on the die surface while promoting consistent pellet quality and production efficiency.
37
How does die temperature affect pellet quality and production efficiency in SERVODAY Ring Die Pellet Mill Machines operation?
Elevated die temperatures in SERVODAY Ring Die Pellet Mill Machines can lead to issues such as reduced pellet density, increased wear on the die surface, and decreased production efficiency, highlighting the importance of proper die cooling and maintenance.
38
What are the benefits of using stainless steel dies in SERVODAY Ring Die Pellet Mill Machines operation?
Stainless steel dies offer advantages such as superior wear resistance, extended lifespan, and reduced maintenance requirements compared to conventional carbon steel dies, making them ideal for high-volume pellet production applications.
39
How does die material hardness affect pellet quality and production efficiency in SERVODAY Ring Die Pellet Mill Machines operation?
Harder die materials in SERVODAY Ring Die Pellet Mill Machines exhibit greater wear resistance and durability, reducing die wear and maintenance costs while maintaining consistent pellet quality and production efficiency in high-volume pellet production operations.
40
What measures can be taken to extend the lifespan of SERVODAY Ring Die Pellet Mill Machines dies?
Implementing proper die alignment, maintenance procedures, and die cooling systems can help extend the lifespan of SERVODAY Ring Die Pellet Mill Machines dies, reducing downtime and production costs in pellet production operations.
41
How does die relief design impact pellet quality and production efficiency in SERVODAY Ring Die Pellet Mill Machines operation?
Optimal die relief design in SERVODAY Ring Die Pellet Mill Machines promotes uniform pellet compression, reduces die wear, and enhances pellet quality and production efficiency in pellet mill operations.
42
What role does die surface finish play in pellet production using SERVODAY Ring Die Pellet Mill Machines?
A smooth die surface finish in SERVODAY Ring Die Pellet Mill Machines reduces friction and wear, promotes uniform pellet compression, and enhances pellet quality and production efficiency in pellet mill operations.
43
What measures can be taken to minimize die wear in SERVODAY Ring Die Pellet Mill Machines operation?
Implementing proper die alignment, maintenance procedures, and die cooling systems can help minimize die wear, extend die lifespan, and improve pellet quality and production efficiency in pellet production operations.
44
How does die wear affect pellet mill performance in SERVODAY Ring Die Pellet Mill Machines operation?
Excessive die wear in SERVODAY Ring Die Pellet Mill Machines can lead to issues such as uneven pellet size, reduced pellet density, and increased energy consumption, negatively impacting pellet quality and production efficiency.
45
What measures can be taken to prevent die rollover in SERVODAY Ring Die Pellet Mill Machines operation?
Implementing regular maintenance schedules, proper die alignment, and monitoring roll-to-die proximity can help prevent die rollover and associated production disruptions in SERVODAY Ring Die Pellet Mill Machines operations.
46
Why is die relief important for pellet production using SERVODAY Ring Die Pellet Mill Machines?
Die relief in SERVODAY Ring Die Pellet Mill Machines facilitates the smooth exit of pellets from the die holes, reducing friction and wear on the die surface while promoting consistent pellet quality and production efficiency.
47
What factors should be considered when selecting the appropriate compression ratio for pellet production using SERVODAY Ring Die Pellet Mill Machines?
Factors such as raw material composition, pellet quality requirements, production volume, and die specifications should be considered when determining the optimal compression ratio for pellet production using SERVODAY Ring Die Pellet Mill Machines.
48
How does die temperature affect pellet quality and production efficiency in SERVODAY Ring Die Pellet Mill Machines operation?
Elevated die temperatures in SERVODAY Ring Die Pellet Mill Machines can lead to issues such as reduced pellet density, increased wear on the die surface, and decreased production efficiency, highlighting the importance of proper die cooling and maintenance.
49
What are the benefits of using stainless steel dies in SERVODAY Ring Die Pellet Mill Machines operation?
Stainless steel dies offer advantages such as superior wear resistance, extended lifespan, and reduced maintenance requirements compared to conventional carbon steel dies, making them ideal for high-volume pellet production applications.
50
How does die material hardness affect pellet quality and production efficiency in SERVODAY Ring Die Pellet Mill Machines operation?
Harder die materials in SERVODAY Ring Die Pellet Mill Machines exhibit greater wear resistance and durability, reducing die wear and maintenance costs while maintaining consistent pellet quality and production efficiency in high-volume pellet production operations.
RING DIE MAKING PROCESS
1
How many machining operations are involved in producing a mid-sized die with 4 mm holes?
A mid-sized die with 4 mm holes undergoes approximately 30,000 machining operations, including drilling, countersinking, counter-boring, and more.
2
What types of chrome steel alloys does SERVODAY offer for SERVODAY Ring Die Pellet Mill Machine dies?
SERVODAY offers a variety of chrome steel alloys tailored to suit various operating environments, with varying content of vanadium, chromium, manganese, nickel, and carbon.
3
How does SERVODAY ensure accuracy and repeatability in the manufacturing process of SERVODAY Ring Die Pellet Mill Machine dies?
With meticulous attention to detail and technical support, SERVODAY follows customer specifications for die hole size, shape, and pattern, ensuring accuracy and repeatability through an automated production process.
4
Why is heat treatment crucial in the production of SERVODAY Ring Die Pellet Mill Machine dies?
Heat treatment is essential as it guarantees product uniformity and maximizes the life of the die. SERVODAY invests in modern hardening technology to produce long-life and high-performance dies.
5
What is gun drilling, and how does SERVODAY utilize this technique in die production?
Gun drilling is a fast and accurate process for producing highly polished extrusion holes. SERVODAY pioneers this technique and optimizes drilling speed and lubricant control to produce the finest pelleting dies.
6
How are machining burrs and contaminants removed from SERVODAY Ring Die Pellet Mill Machine dies before heat treatment?
Before heat treatment, oil, moisture, and machining burrs are meticulously removed from the die surface through washing and polishing processes.
7
What is CNC machining, and how is it employed in die production?
CNC machining centers, programmed with die dimensions for all SERVODAY Ring Die Pellet Mill Machine makes and models, machine the basic shape of the die with precision accuracy.
8
What is vacuum hardening, and why is it important in SERVODAY Ring Die Pellet Mill Machine die production?
Vacuum hardening creates a hard-wearing surface in the die holes, maximizing die lifespan. The process involves heating the die in stages to a temperature of 1,010 °C, resulting in a hard molecular structure.
9
How are SERVODAY Ring Die Pellet Mill Machine dies inspected for quality assurance before dispatch?
Quality-assured systems monitor the product throughout the manufacturing process. In the final stage, the dies are machined to fit the pellet mill perfectly, and a final inspection ensures conformity to specifications before dispatch.
10
What raw materials are used in the production of high-quality SERVODAY Ring Die Pellet Mill Machine dies?
Selected high-quality steels with fine grain structures are used to ensure high strength and durability in SERVODAY Ring Die Pellet Mill Machine dies.
11
How does automated countersinking contribute to pelleting performance in SERVODAY Ring Die Pellet Mill Machine dies?
Automated countersinking, carefully following the drill pattern, enhances pelleting performance by machining countersinks into the die track, selected to optimize performance.
12
What is the significance of finishing and final inspection in the manufacturing process of SERVODAY Ring Die Pellet Mill Machine dies?
Finishing and final inspection ensure that SERVODAY Ring Die Pellet Mill Machine dies are machined to fit perfectly and meet original specifications before dispatch, guaranteeing quality and performance.
13
Why does SERVODAY invest in modern hardening technology for SERVODAY Ring Die Pellet Mill Machine die production?
SERVODAY invests in modern hardening technology to produce long-life and high-performance SERVODAY Ring Die Pellet Mill Machine dies, ensuring product uniformity and durability.
14
How does heat treatment contribute to the uniformity of SERVODAY Ring Die Pellet Mill Machine dies?
Heat treatment is crucial as it establishes uniformity in SERVODAY Ring Die Pellet Mill Machine dies, guaranteeing consistent performance and longevity.
15
What are the advantages of gun drilling in the production of SERVODAY Ring Die Pellet Mill Machine dies?
Gun drilling offers fast and accurate drilling, producing highly polished extrusion holes essential for efficient pelleting. SERVODAY utilizes this technique to optimize die quality and performance.
16
How does CNC machining enhance the precision of SERVODAY Ring Die Pellet Mill Machine dies?
CNC machining centers programmed with die dimensions ensure precise shaping of SERVODAY Ring Die Pellet Mill Machine dies, contributing to their quality and performance.
17
What role do raw materials play in ensuring the strength and durability of SERVODAY Ring Die Pellet Mill Machine dies?
Selected high-quality steels with fine grain structures provide the necessary strength and durability for SERVODAY Ring Die Pellet Mill Machine dies to withstand demanding operating conditions.
18
How does vacuum hardening improve the lifespan of SERVODAY Ring Die Pellet Mill Machine dies?
Vacuum hardening creates a hard-wearing surface in the die holes, maximizing die lifespan and performance in pellet production.
19
Why is meticulous attention to detail important in the manufacturing process of SERVODAY Ring Die Pellet Mill Machine dies?
Meticulous attention to detail ensures accuracy and repeatability in the production of SERVODAY Ring Die Pellet Mill Machine dies, guaranteeing quality and performance in pellet production.
20
What steps are involved in the final inspection of SERVODAY Ring Die Pellet Mill Machine dies before dispatch?
In the final inspection stage, SERVODAY Ring Die Pellet Mill Machine dies are machined to fit perfectly and undergo rigorous checks to ensure conformity to original specifications, ensuring quality and reliability in pellet production.